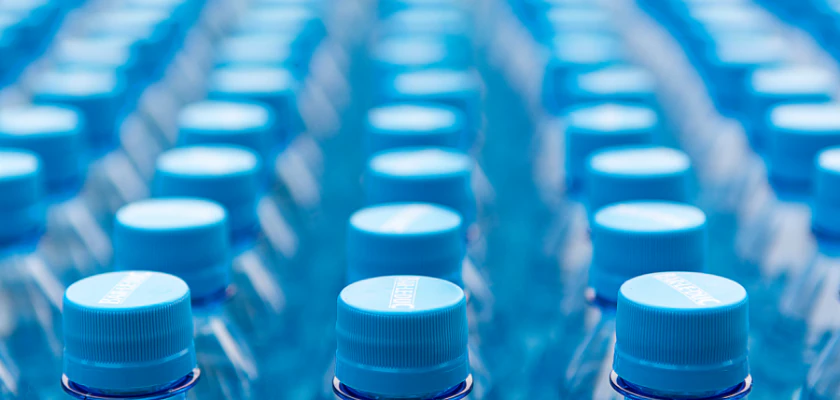
Termoform Plastik Süreci için Kapsamlı Bir Kılavuz
Bir üretim işlemi olan termoform plastik, sıklıkla tercih edilen bir prosestir. Isı ile şekillendirmeyle başlayan bu proses, iki ana türe ayrılır. Düşük maliyetli olmasına karşın büyük parça üretimine olanak sağlama gibi avantajlar sunan bu prosesin avantajları ve bu sürece kapsamlı bir bakış için yazının devamını okuyabilirsiniz.
İçindekiler
ToggleTermoformu Anlamak: Sürece Kapsamlı Bir Bakış
Termoform plastik üretim süreci, ısı ile şekillendirmeyle başlar. Kullanılacak olan plastik tabaka, bükülebilecek duruma gelene dek ısıtılır. Sonrasında prosese uygun bir kalıp kullanılarak şekil verilir. Buna uygun olarak kesilir ve katı bir forma gelene dek tekrar soğutulur. Bu üretim sürecinde kullanılan kalıp, esasen plastik enjeksiyon kalıplama gibi bir kalıptır. Fakat aralarında temel bir fark vardır. Bu fark plastiğin tamamen eritilmemesi ve yumuşak bir halde olsa da katı halde olmasıdır. Prototipler veya daha küçük sipariş boyutları oluştururken genellikle plastikler ısıyla şekillendirilir. Fakat daha büyük siparişlerde de sürekli ve yüksek hızlı bir süreçle elde edilmesi mümkündür.
Termoform Plastik Prosesinin Keşfi: Ayrıntılı Bir Açıklama
Termoform plastik, iki ana türe ayrılabilir. Bunlar vakumla şekillendirme ve basınçla şekillendirme prosesleridir.
Vakum şekillendirme prosesinde, plastik tabakaların bir kalıp üzerinde şekillendirilmesi için ısı ve basınç kullanılır. Bu yöntemde stabil ve tam bir şekil sağlanır. Elbette bazı dezavantajları da vardır. Vakum şekillendirme yönteminde plastikte kabarcık oluşumu yaşanabilir ve plastiği zayıflatma ihtimali daha yüksektir. Bu dezavantajın üstesinden gelebilmek için işleme başlamadan önce plastik çok daha uzun süreler boyunca kurutulur. Bunun yanında bu prosesin diğer riskleri, plastikte aşınmalara neden olması ve kalıbı oluşturan bölümlerin birbirine çok yakın olması halinde ağ oluşumuna imkan sağlamasıdır.
Bir diğer tür olan basınç oluşturma, vakum şekillendirme yöntemine çok benzer. Fakat diğer yöntemden farklı kılan ilave basınç gerektiriyor olmasıdır. Tabakanın kalıpsız kısmına bir basınç kutusu eklenir. Bunun nedeni 60 pound psi’ye varana kadar daha fazla basınç oluşturmaktır. Böylelikle prosesin sonunda daha keskin, daha karmaşık ayrıntılar elde etmek mümkün olur. Sağladığı bu avantaja ek olarak tıbbi ekipman ve çok parçalı montajlar gibi daha fazla ayrıntı ve dikkat gerektiren uygulamalar için ideal bir yöntemdir.
Termoform Plastik Tercihi: Seçimin Arkasındaki Nedenleri Ortaya Çıkarmak
Plastik termoform diğer plastik, metal ve FRP üretim yöntemlerine kıyasla pek çok avantaja sahiptir. Dolayısıyla bu prosesin uygulanmasının ardında aslında pek çok neden vardır. Bu nedenleri şu şekilde sıralamak mümkündür:
- Düşük maliyetli olmasına karşın büyük parça üretimine olanak sağlaması,
- Isıyla şekillendirilmiş plastiklerin çeliğe kıyasla 6 kat daha hafif olması,
- Sağlam olması ve buna ek olarak birbirinden farklı pek çok sektör ile uyumlu malzeme üretebilme olanağı sunması,
- Düşük maliyetle yüksek detaylı parçalar üretimine olanak sağlaması,
- Çok parçalı montaj ve projeler yapılabilmesi,
- Yılda yaklaşık 250-5000 parçalık düşük ya da orta hacimli ürün üretimi sağlaması,
- Düşük takım yatırımı gerektirmesi,
- Hızlı ürün geliştirmeye olanak sağlaması,
- Tasarım estetiği sunması ve sağladığı markalama yetenekleri.
Tüm bu nedenler termoform plastiğin sıklıkla tercih edilmesinin nedenleri arasında gösterilebilir.
Potansiyelin Kilidini Açmak: Termoform Plastik Uygulamaları ve Olanakları
Termoform plastik prosesi çok yönlü ve düşük maliyetli bir proses olduğundan birçok endüstri uygulamaları için sıklıkla tercih edilir. Isıyla şekillendirilmiş parçalardan fabrikasyon metal levha bileşenlerine bir alternatif olarak da yararlanılır. Bunun yanında FRP yöntemi (elyaf takviyeli plastikler) kullanılarak oluşturulan parçalara kıyasla çok sayıda avantaj sunan bir prosestir. Hem yeni tasarım projelerde hem de mevcut tasarımdan proses dönüşümlü projelerde rahatlıkla tercih edilebilir. Dolayısıyla sayısız uygulama ve endüstri için kullanılabilir.
Isıyla Şekillendirme için Plastik Seçimi: Uygun Malzemelerin Belirlenmesi
Plastik içeren diğer işlemlerde olduğu gibi termoform plastik işleminde de çeşitli polimerler kullanılır. Bunların arasında en yaygın olarak tercih edilen plastik türleri şu şekilde sıralanabilir:
- ABS Plastik (akrilonitril, bütadien, stiren): Bu plastik ısı direnci ile bilinir ve yüksek sıcaklıklarda kullanım için idealdir. Özellikle boru sistemleri, golf sopası başlıkları, müzik aletleri ve oyuncaklar için sıkça tercih edilir.
- Akrilik: Isıyla şekillendirildiği takdirde sert ve kırılgan olmasına karşın muntazam bir şekilde katlanabilir bir hale geldiğinden dolayı sıklıkla tercih edilir. Elementlere karşı dayanıklıdır ve birçok rengi mevcuttur. Otomotiv bileşenlerinde ve kişisel koruyucu ekipmanlarında kullanılır.
- HDPE (yüksek yoğunluklu polietilen): Petrolden yapılır ve oldukça sağlamdır. Özellikle plastik poşetler, su boruları ve spor aletlerinde kullanılır.
- PET Plastik (polietilen tereftalat): Dayanıklıdır ve bunun yanında kimyasallara, ısıya karşı yüksek mukavemet gösterir. Bu özelliklerinden ötürü sıklıkla tercih edilir. Kolaylıkla geri dönüştürülebilir olmasından dolayı sürdürülebilir bir malzemedir.
- PVC Plastik (polivinil klorür): Isıya ve basınca karşı yüksek mukavemet gösteren, sağlam ve dayanıklı bir yapıya sahiptir. Bu avantajlarının yanında üretim maliyeti oldukça düşüktür. Borular, kablolar, bilgi tabelaları ve buna benzer birçok günlük kullanımı mevcuttur.
Çeşitli Kullanım Alanlarını Keşfetmek
Sayılan kullanım alanlarına ek olarak, sağladığı avantajlar sayesinde termoform prosesi, pek çok sektör ve endüstride sıklıkla tercih edilir. Bu endüstri ve sektörler aşağıdaki gibi sıralanabilir:
- Tıbbi cihaz ekipmanları için kullanılan muhafazalar,
- Döşeme, panel, pencere maskeleri, oturma yerleri, tepsi masaları, bagaj rafları ve daha birçok vagon iç parçaları,
- Endüstriyel taşımalar ve inşaat araçları için iç dış kaplamalar ve paneller,
- Kioks, ATM ve POS uygulamaları için ön panolar ve muhafazalar,
- Yemek servisi bileşenleri,
- Taşıma tepsileri ve malzeme taşıma bileşenleri,
- Kamyon yatak örtüleri,
- Atık su yönetim bileşenleri,
- Portatif tuvalet bileşenleri,
- Büyük ekipman muhafazaları,
- Tarımla alakalı ekipmanlar ve araç bileşenleri.
Artıları ve Eksileri Tartmak: Avantajları ve Dezavantajları
Diğer tüm proseslerde olduğu gibi termoform plastik sürecinde de bazı avantajlar ve dezavantajlardan bahsetmek mümkündür. Öncelikle bu plastik süreci son derece uyarlanabilir bir süreçtir. Birçok farklı tasarım boyutu, şekli ve karmaşıklığı sunduğundan müşteri spesifikasyonu açısından yeterlidir. Ürün maliyetleri düşüktür ve dolayısıyla prototip oluşturmak için ideal bir işlemdir. Nihai parçalar çekici olmasının yanında dayanıklıdır. Ayrıca aynı plastik kaplama veya reçine topaklarıyla birkaç farklı ürün oluşturmaya olanak sağlar.
Bu avantajların yanında bazı dezavantajlardan da bahsedilmesi gerekir. Termoform plastik prosesi, yalnızca ince duvarlı ürünler ile kullanıma uygundur. Bunun yanında proses süresince kabarcık ya da ağ oluşumu riski de söz konusudur. Fakat daha önce de değinildiği gibi bu riskleri ortadan kaldırmak için pek çok yöntem mevcuttur.
